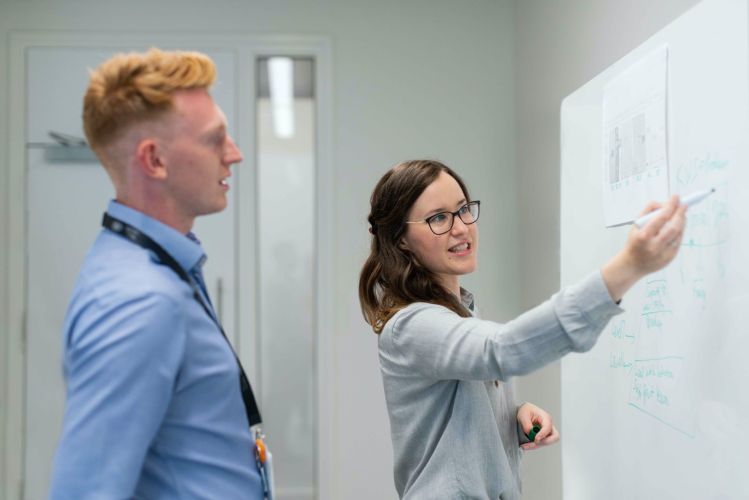
Predictive Analytics in Manufacturing
Manual operations in manufacturing often lead to higher costs and lower growth rates. Manufacturers have four critical challenges to address: optimizing processes, reducing costs, improving product quality, and predicting demand.
Digitizing one or two processes can only partially help, and only a complete digital solution can be helpful. Especially critical tasks such as demand forecasting require a robust forecasting system based on operational data analysis, and without that, manufacturers will never be able to plan for the future.
An exciting yet best way to overcome this problem is to automate the process with predictive maintenance solutions.
Let’s get into the applications of predictive maintenance in manufacturing: improving operations and product quality while reducing costs and predicting future demand.
A predictive maintenance system includes the Internet of Things, the cloud, mobile apps, AI/ML, and a web application.
The system works as follows. Initially, data will be collected by IoT devices installed on machines or assets.
The data will be processed in the cloud or sent to the relevant individuals as notifications/warnings or alerts.
The processed data will be put into the AI/ML system, assessing and forecasting the outcomes of the data gathered over time.
Prediction reports will be shared with the appropriate stakeholders for necessary actions or decisions.
The benefits of predictive maintenance for manufacturing
- Accurate, real-time collection of equipment status data
- Anticipating and predicting equipment downtime in advance
- Increased transparency
- Reduced production delays
- Increased production on schedule
- Reduced maintenance costs
- Anticipate equipment failures
- Reduced repair costs
- Increase in service life and utilization of equipment
- Increased employee safety
- Increase in total profits
- Demand Forecasting
By now, you are familiar with the basics of Predictive Maintenance and its benefits.
Let’s delve into a discussion of how Predictive Maintenance is transforming manufacturing operations and production growth.
Predictive maintenance to improve operations
Operational efficiency plays a crucial role in the pace and quality of production. Because it involves people, machines, and technology, optimizing all of this is essential for problem-free production that meets expected results.
Before you get started, you need to understand what problems affect production efficiency.
The performance of machines operating at different levels (peak, average or normal) must be analyzed. Machine efficiency is essential when it comes to improving operational efficiency. Only when machines are fully utilized and working at their best can maximum productivity be achieved.
This requires tracking the performance of each machine and its every movement. The IoT is used to collect data, and by analyzing historical data, faults or inefficiencies in operation are identified and corrected.
In addition, IoT-enabled predictive maintenance systems can be used to predict problems that may occur in the future.
Typically, overall equipment efficiency (OEE) is calculated using IoT data and analyzed and improved to make the operation efficient and profitable.
Another scenario could be the resource productivity of machines. It needs to be identified and addressed to improve staff efficiency. Digitalizing the process with Industry 4.0 solutions, such as IoT, can improve overall efficiency.
Predictive maintenance for machine use and management
Unscheduled machine maintenance costs most manufacturing companies more money, so the process must be monitored and controlled to maximize productivity.
Failures or faulty machines affect production in two ways – first, they reduce product quality, and second, they incur recurring repair costs.
So you need to discover a means to uncover machine inefficiencies and enhance their efficiency before a costly breakdown happens.
In a predictive maintenance system, the data collected from each machine move provides a significant amount of data to be analyzed with AI/ML software to identify machine failures and malfunctions.
The predictive maintenance system provides data on the current state of the asset, its availability, and defect information to help you rethink production plans.
With this approach and data trends, anticipating and predicting machine failures as early as possible leads to lower repair costs and maintenance labor. This could potentially save millions for your business.
Predictive maintenance for production quality
Even though predictive maintenance or IoT don’t directly impact product quality or production rates, the combination of the two can make a big difference in overall production levels.
Because IoT can help optimize the performance of machines, people, and technology. Predictive maintenance will take care of machine efficiency – expecting improvements in quality and speed of production will never be a problem for manufacturers.
Predictive maintenance for demand forecasting
The ultimate benefit of predictive maintenance for manufacturers is demand forecasting.
Because manufacturers have tons of data, but no insight, the process of improvement and planning always stalls. It is easy to anticipate what can be done in the coming years with a predictive maintenance system based on historical data.
Because a predictive maintenance system eliminates siloed data and creates 100% transparency across the entire manufacturing enterprise, it’s never possible to know what the current situation is and what to expect in the future.
By planning ahead of time and understanding what to expect, you can rapidly estimate the efficiency of machinery, staff, and repair expenses in order to plan for future goals that will be feasible.
An example of using predictive maintenance – is the asset management
Predictive maintenance has many uses in the manufacturing industry, especially in asset condition monitoring.
There may be scenarios where assets will be operated at different temperatures, and monitoring their performance in various conditions is a must to maintain quality and speed of production.
These types of assets must be constantly monitored to keep them in good shape, and even minor malfunctions or defects can cost a company millions of dollars.
With predictive maintenance, monitoring assets under different conditions is seamless, and the historical data obtained can help predict future asset performance and determine when they will need replacement or maintenance.
Predictive maintenance helps determine:
- When an asset needs to be replaced
- When the asset needs maintenance
- How long it will be effective
- When it is likely to fail
- What is the cause of failure
- What is the risk associated with failure
- What maintenance would be practical to improve the use of the asset
- The return on investment in predictive maintenance
Final Thoughts
It follows from the above that predictive analytics is a boon to manufacturers because it reduces maintenance costs, improves operational efficiency and product quality, and helps plan for future programs.
Predictive analytics is evolving, and the latest addition to predictive analytics, prescriptive analytics, is gaining momentum in the industrial landscape.
The latter is a subcomponent of predictive analytics and provides data on what is causing equipment failure and recommendations on fixing the fault or defect.
With too many companies investing in predictive maintenance systems, it’s time for you to decide to keep up with the competition. Start now, before one of your competitors does.